SERVICES
In order to facilitate the introduction of efficient laser processing into companies, Novika offers a wide range of unique services in the field of industrial processes using high-powered lasers :
- Transfer of technology information;
- Prototype realisation;
- Assessment of the relevance of the technology within a business;
- Development and adaptation of technology;
- Implementation support: equipment selection, product optimization for the technology, start-up, training, technical support, safety and maintenance.
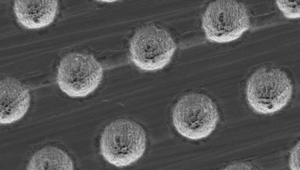
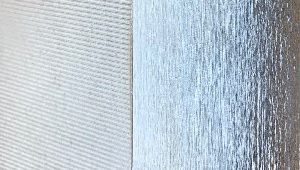
RECENT PROJECTS
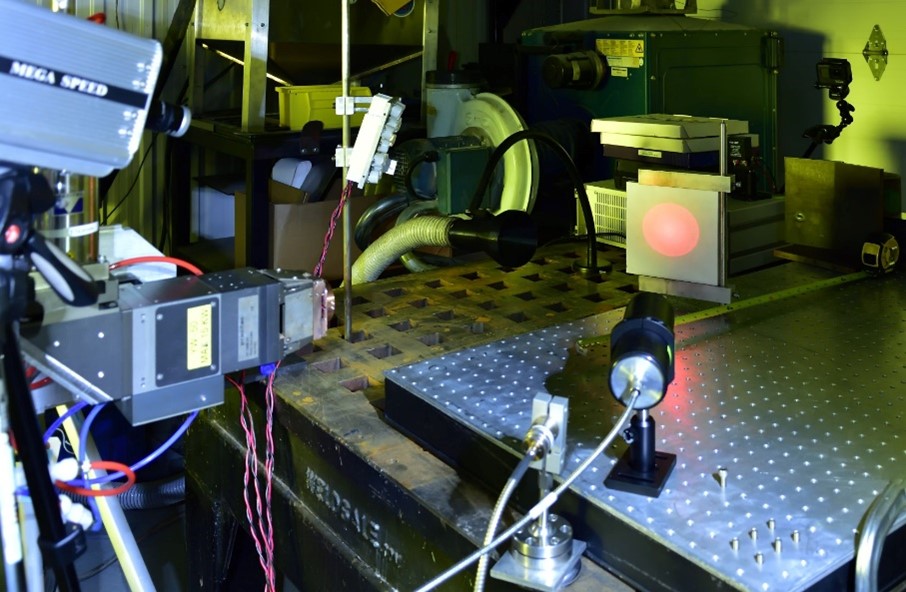
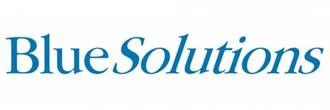
Developing complex component welding parameters for primary and secondary electrochemical generators requiring a perfect seal for the energy storage industry. Novika has tested multiple welding techniques and came up with a stable process that ensures predictable high quality results.
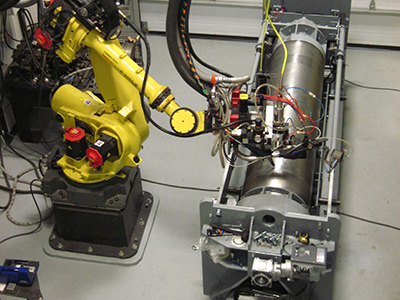
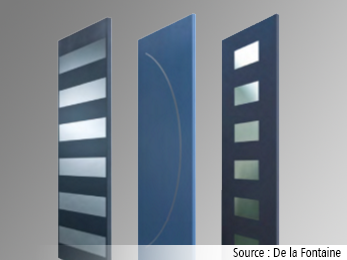
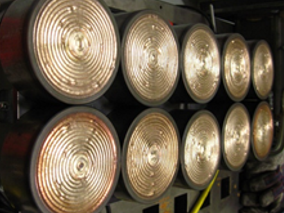
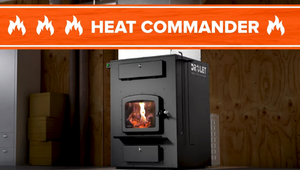
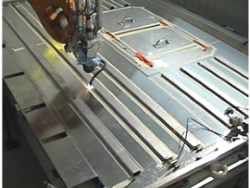
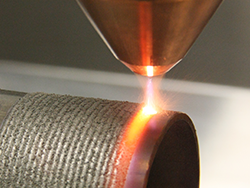
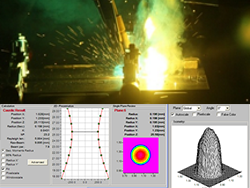
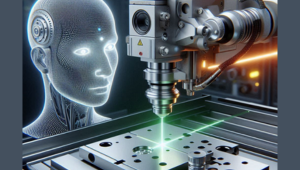
Laser Micromachining Parameter Prediction Using AI (FR)
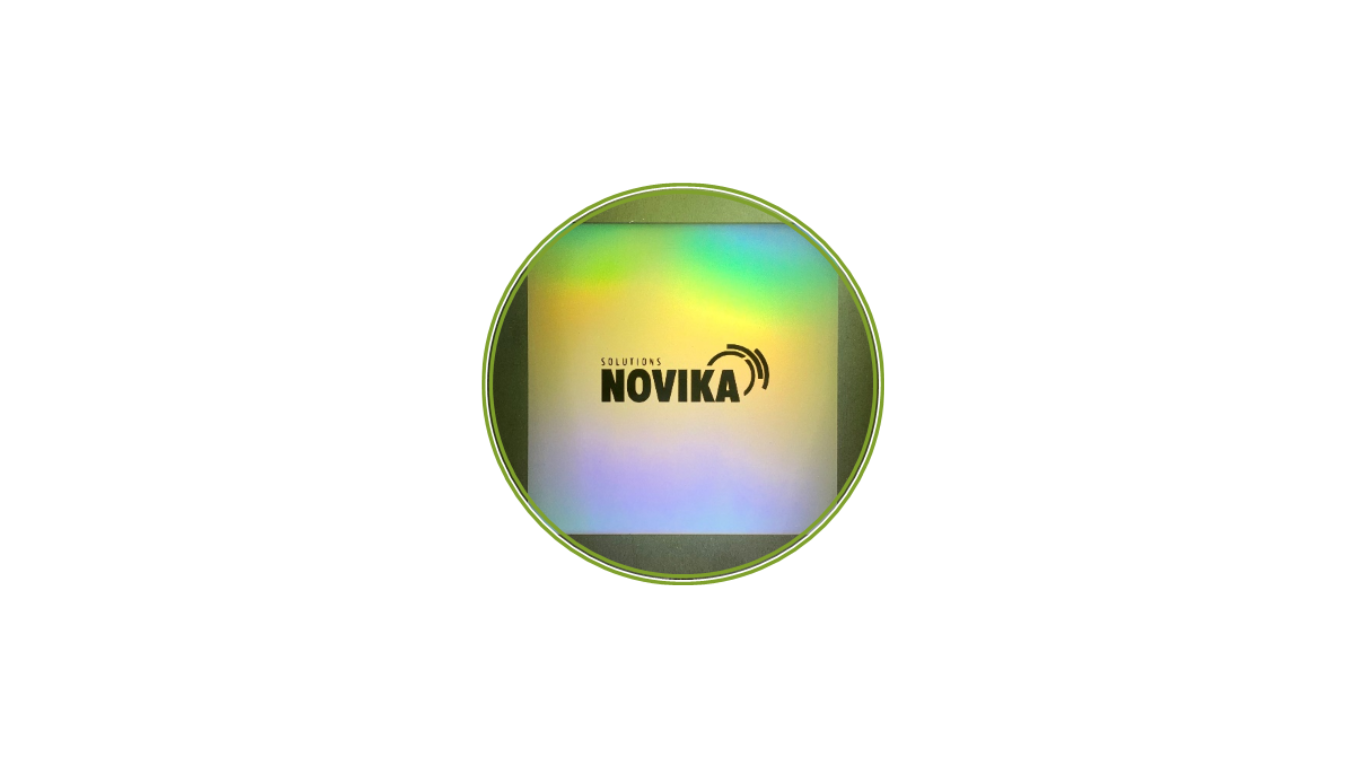
TEAM
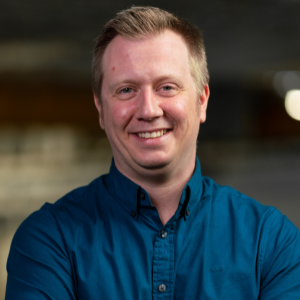
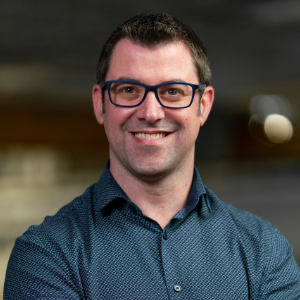
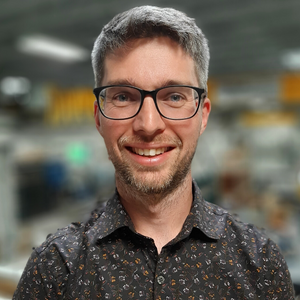
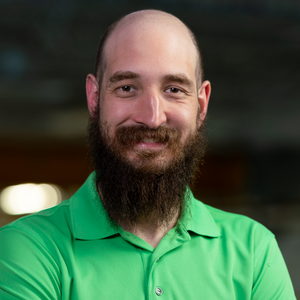
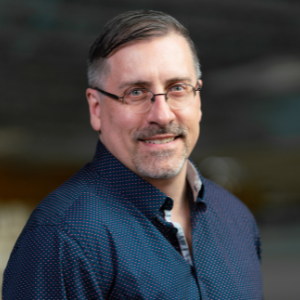
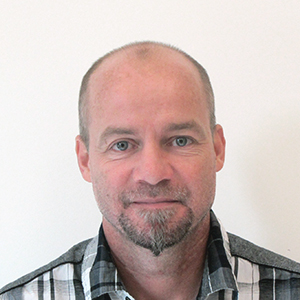
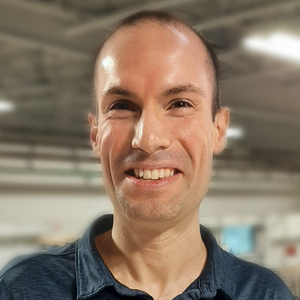
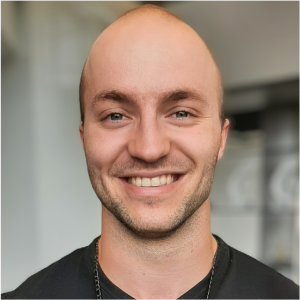
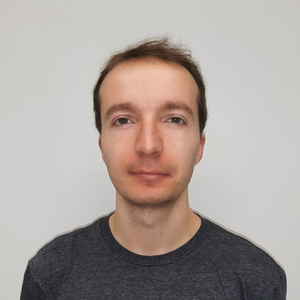
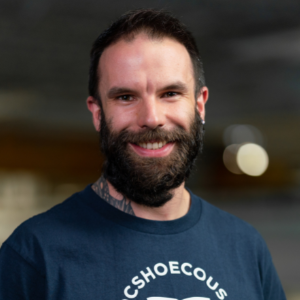
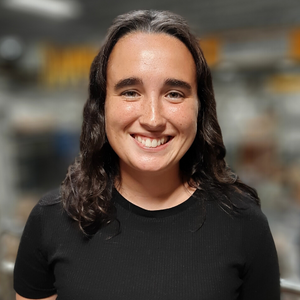
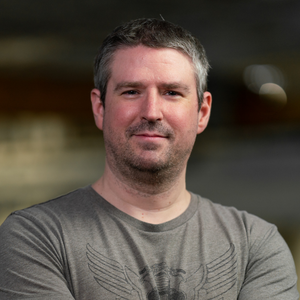
EQUIPMENT
Novika's laser lab is constantly evolving to offer you the technologies that are best adapted to your needs.
Presentation of our laser sources (FR)
Laser sources
Continuous emission (can be modulated in long pulses) :
- 15 kW CW fiber laser (1 070 nm)
- 2 kW CW fiber laser (1 070 nm)
Short pulses :
- 100W 600 µs CO2 laser (10 600 nm)
- 100W 100 ns fiber laser (1 070 nm)
Ultra-short pulses :
- 25 W 9 ps YAG laser (1 064 nm)
- 20 W 350 fs fiber laser (1 030 nm)
- 10 W 350 fs fiber laser (515 nm)
Laser heads
- Laser welding, transmissive and reflective optics
- Hybrid laser/GMAW welding
- Scanner
- Laser cladding with powder, cold wire and hot wire
- Laser cutting
Positioning
- 6-axis robots up to 165 kg
- 1 and 2 axis servo positioners
- Precision linear and rotary axes (0,5µm resolution, 1µm repeatability)
- Joint tracking systems with adaptive platform
- Positioning cameras
Diagnostic and measurements equipment
- Power meter
- Beam monitor
- High speed cameras
- Spectrometer
- Pyrometer
- Thermal camera
- Microscopes
- Data acquisition systems